The most popular printing system for large print runs to date is offset printing. Offset printing, although much more sophisticated and mechanized, is based on the same principle as lithography, a technique devised in 1790 by Alois Senefelder, whereby water and grease repel each other.
Lithography makes use of porous limestone, offset printing of aluminum plates; lithography “writes” the matrix with a grease pencil and then immerses it in a liquid to acidify it in all the unwritten parts, offset printing, on the other hand, uses a laser that directly makes the printing areas water-repellent; in both techniques, the matrices are glazed with water, which settles only in the unprinted areas, and then covered with ink, which, on the contrary, settles only where there is no water. Underlying both techniques is the phenomenon of chemical/physical repulsion between water and ink.
While offset printing can be practiced only with professional machinery, lithography can be recreated more easily, but it still presents two problems that make it impractical and inaccessible: the difficulty in finding and transporting the stone and the dangerousness of the acids used in the process.
To allow beginners and children to experiment with the basic principle of lithography anyway, artist Émilie Aizier in 2011 devised a very cheap and safe alternative method that uses materials and substances found in many kitchens: aluminum foil, cola, vegetable oil and little more. Hence the name Kitchen Litho.
Need
A small sheet of glass or plexiglass (for example, the glass of a picture frame), which will serve as a matrix
Oil-based printing ink (for example, intaglio ink)
An inking roller
Adhesive tape
Drawing materials, a grease pencil (e.g., an 8B), some graphite, oil pastels, carbon paper, some butter, Marseille soap, etc.
Aluminum foil
A basin
Cola
Seed oil
Cloth sponges and cloth
Sheets to print on
Optional: latex gloves
1.Coating the glass plate
The first step in the process is to coat the glass or plexiglass plate, with aluminum foil, securing it with adhesive tape and taking care that no holes remain through which the cola could pass. The aluminum foil should be placed with the opaque side on the outside.
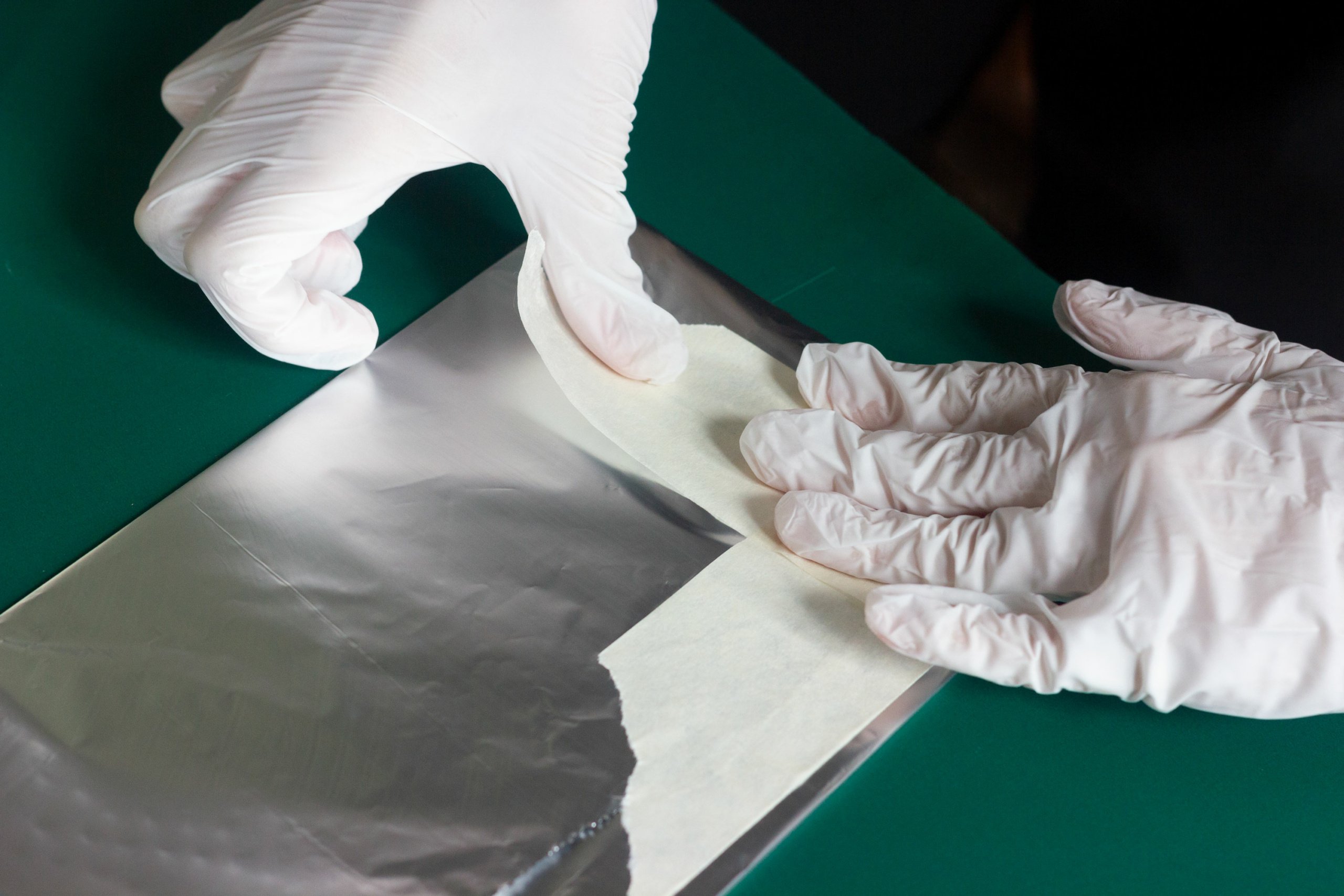
In carrying out this operation, it is very important not to touch the side that will be used for printing with your fingers. In fact, finger grease would risk leaving an imprint then visible in the prints.
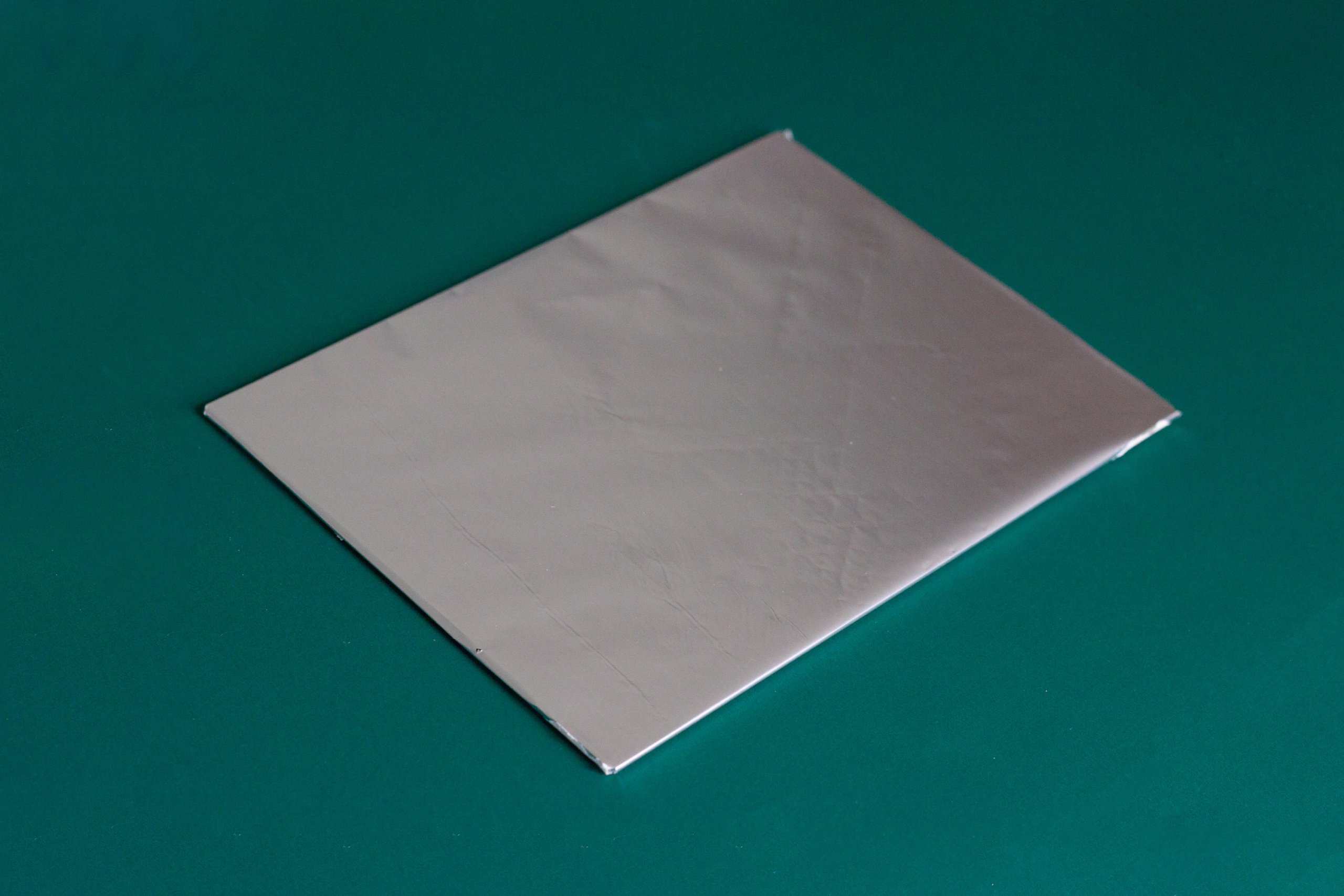
2.Drawing on the plate
The plate is now ready to be imprinted. The die to be printed is drawn directly on the aluminum, and any greasy material will do. As a first approach it is useful to test different materials: certainly grease pencils and graphite are a good option, but it is also worth trying oil pastels or even Marseille soap or butter, using a small brush. Any other greasy material you have on hand may prove useful.
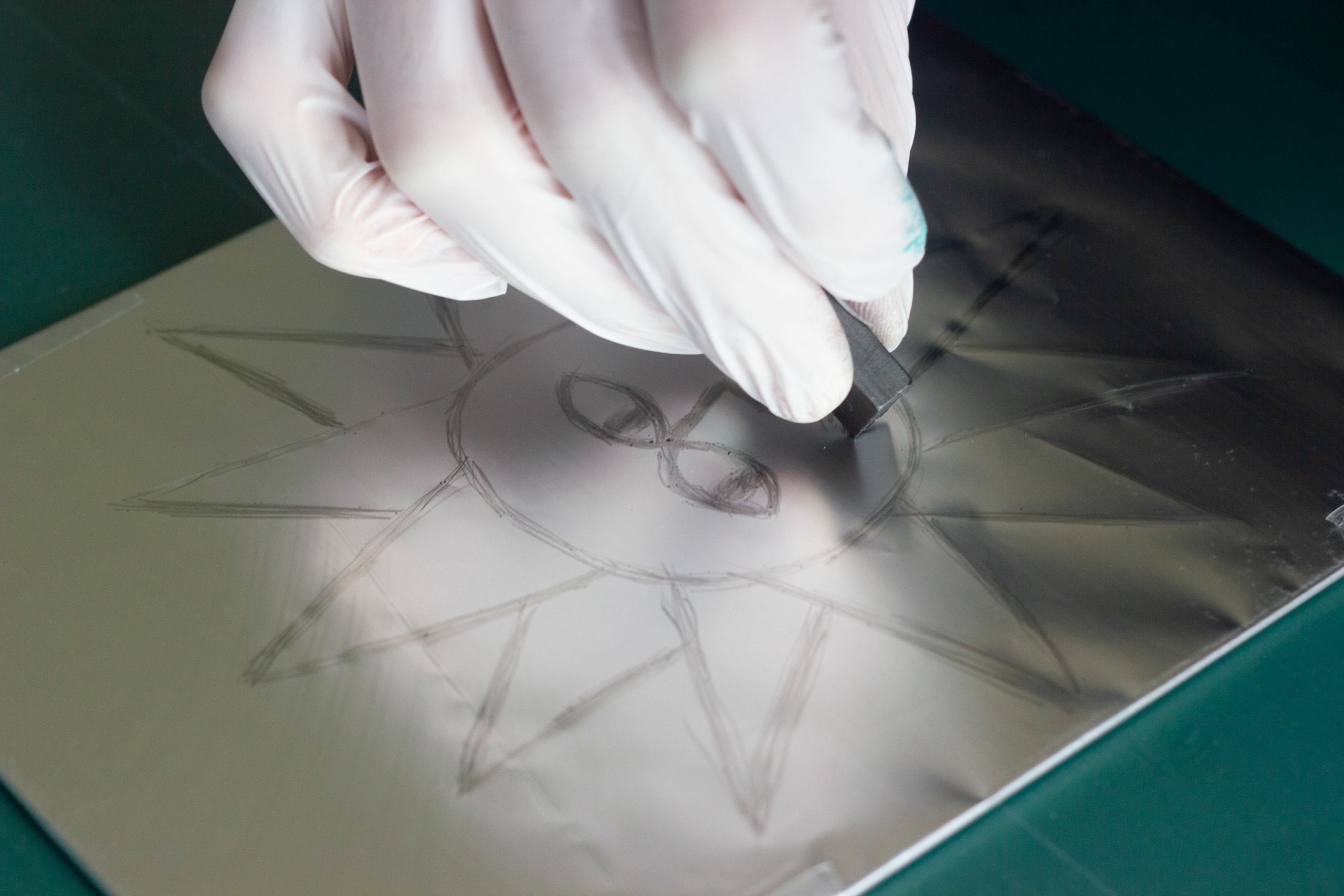
As in the previous step, care should be taken not to touch the plate with your fingers while drawing. It may be helpful to wear latex gloves.
3.Acidify the slab
When the drawing is finished, the slab should be placed in a basin or tub, where you pour cola over it. It is helpful to rotate the slab, and pour the cola, in each direction so that all nonprinting areas are acidified.
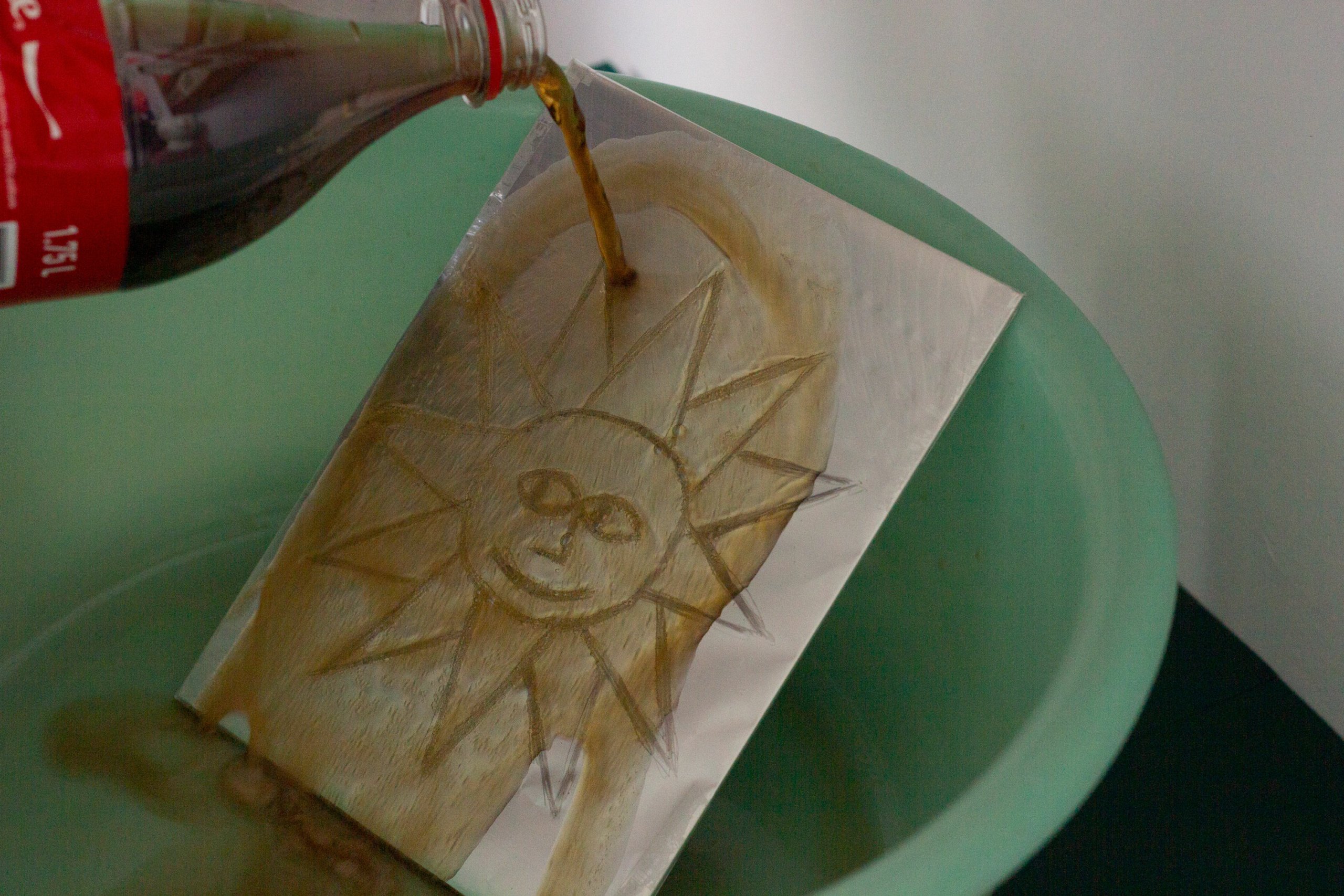
In places where grease is present you can see that the cola does not adhere, but creates bubbles.
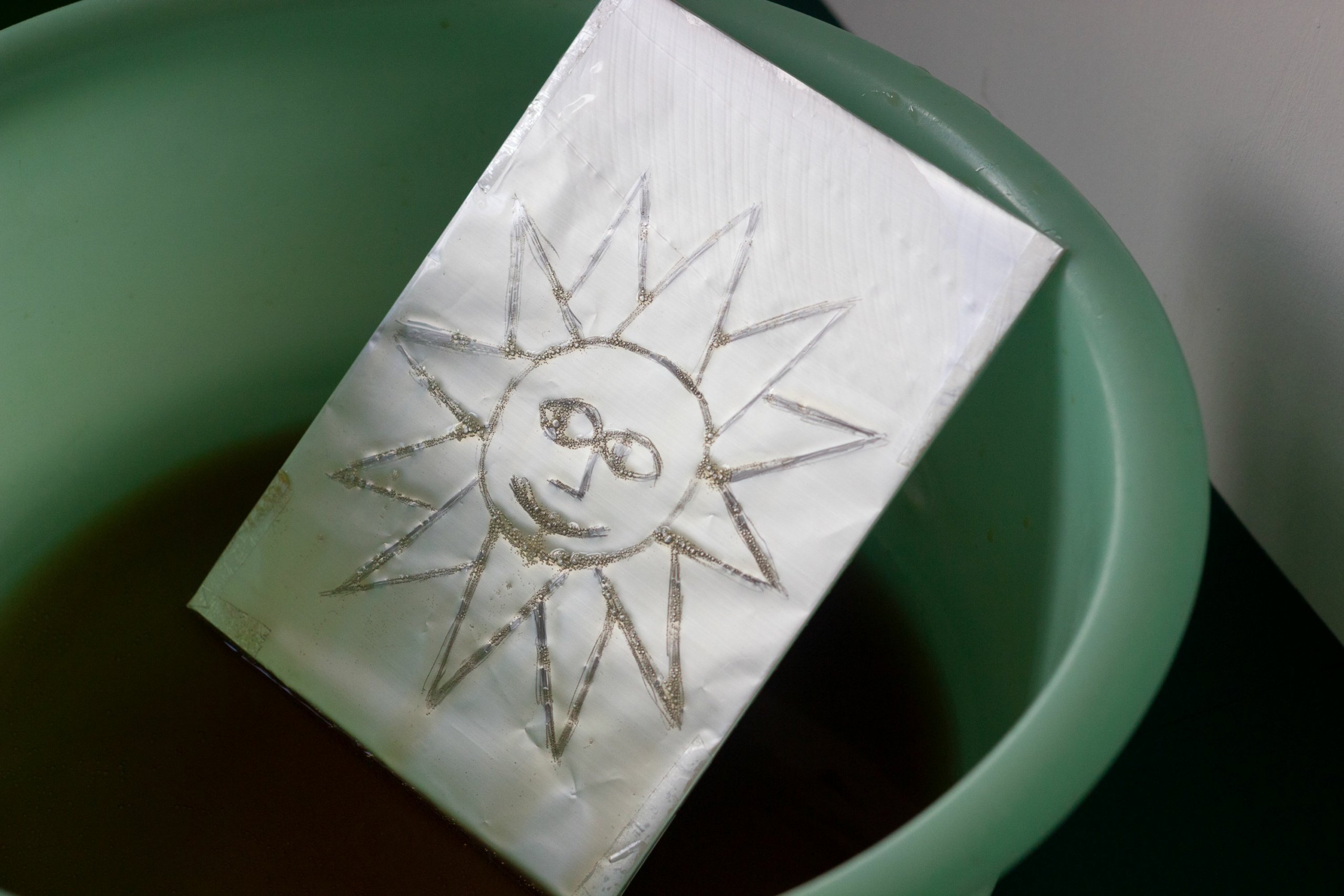
4.Clean the plate
Simply leave the plate under the cola for a few seconds, and then you can proceed to wipe it with a wet sponge to remove the liquid residue. So, with a cloth soaked in vegetable oil, gently wipe the plate clean of any remaining graphite residue or other greasy material that would clog the ink.
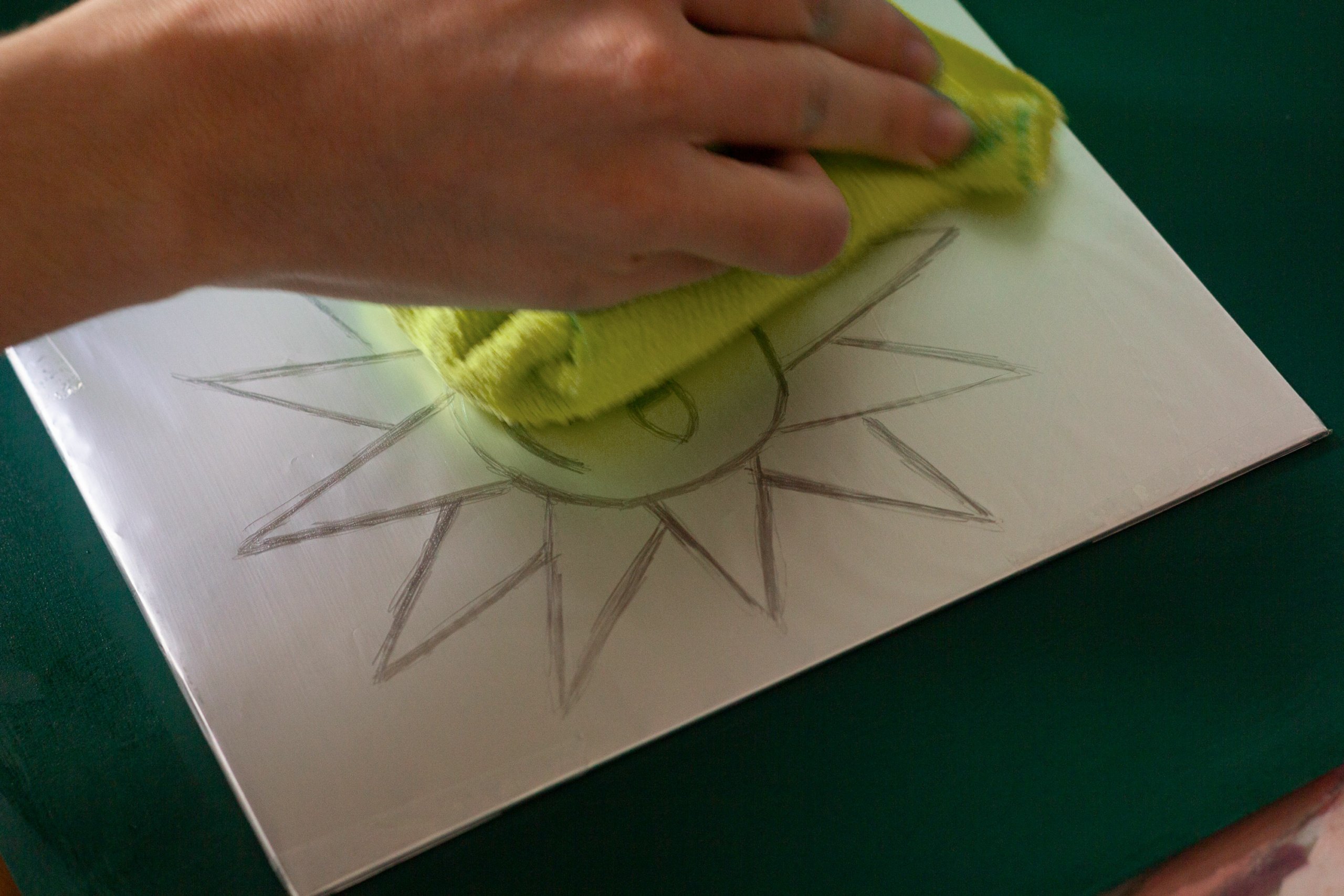
At this point the faded image should remain visible on the aluminum.
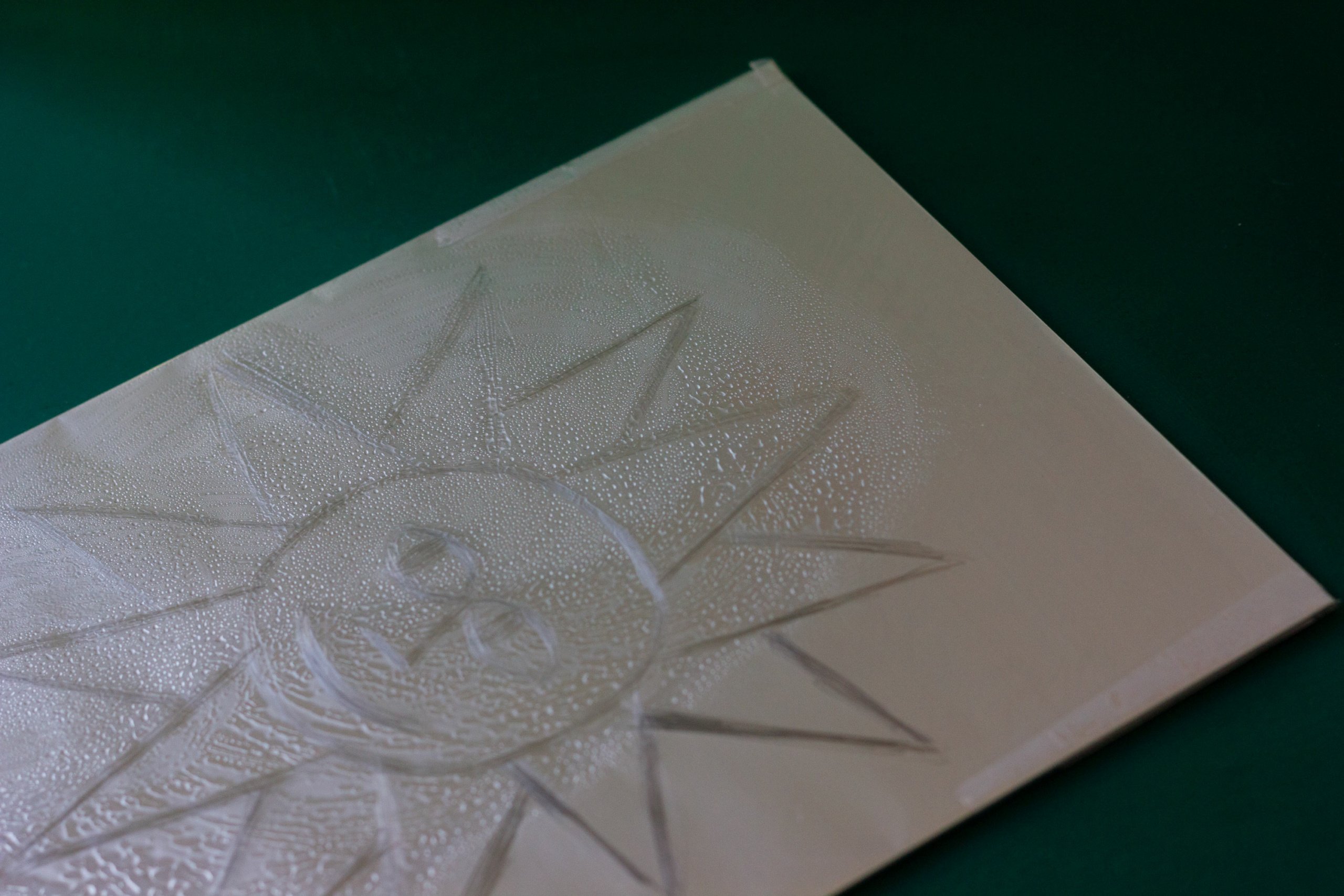
5.Inking
Next comes the preparation of the ink. The color suitable for this type of process is very greasy and thick, like that for intaglio, so it must be spread on a plate and passed over it with the roller in different directions for a few minutes until it is smooth and even.
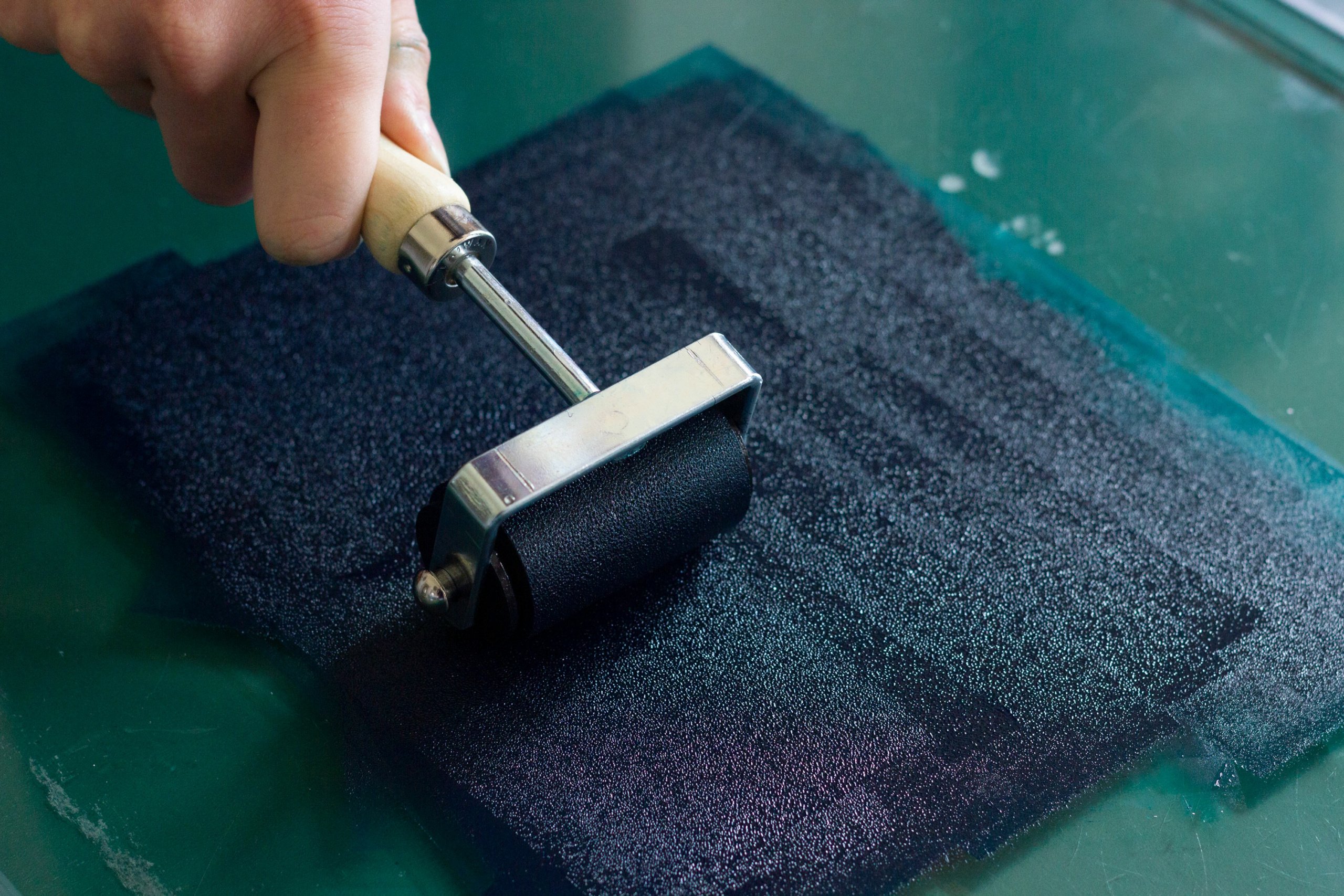
The phosphoric acid and gum arabic in the cola make the areas of the plate that have not been drawn hydrophilic. Once the plate is wet therefore, the water settles on these areas, but is repelled by the drawn areas, where the greasy ink settles instead.
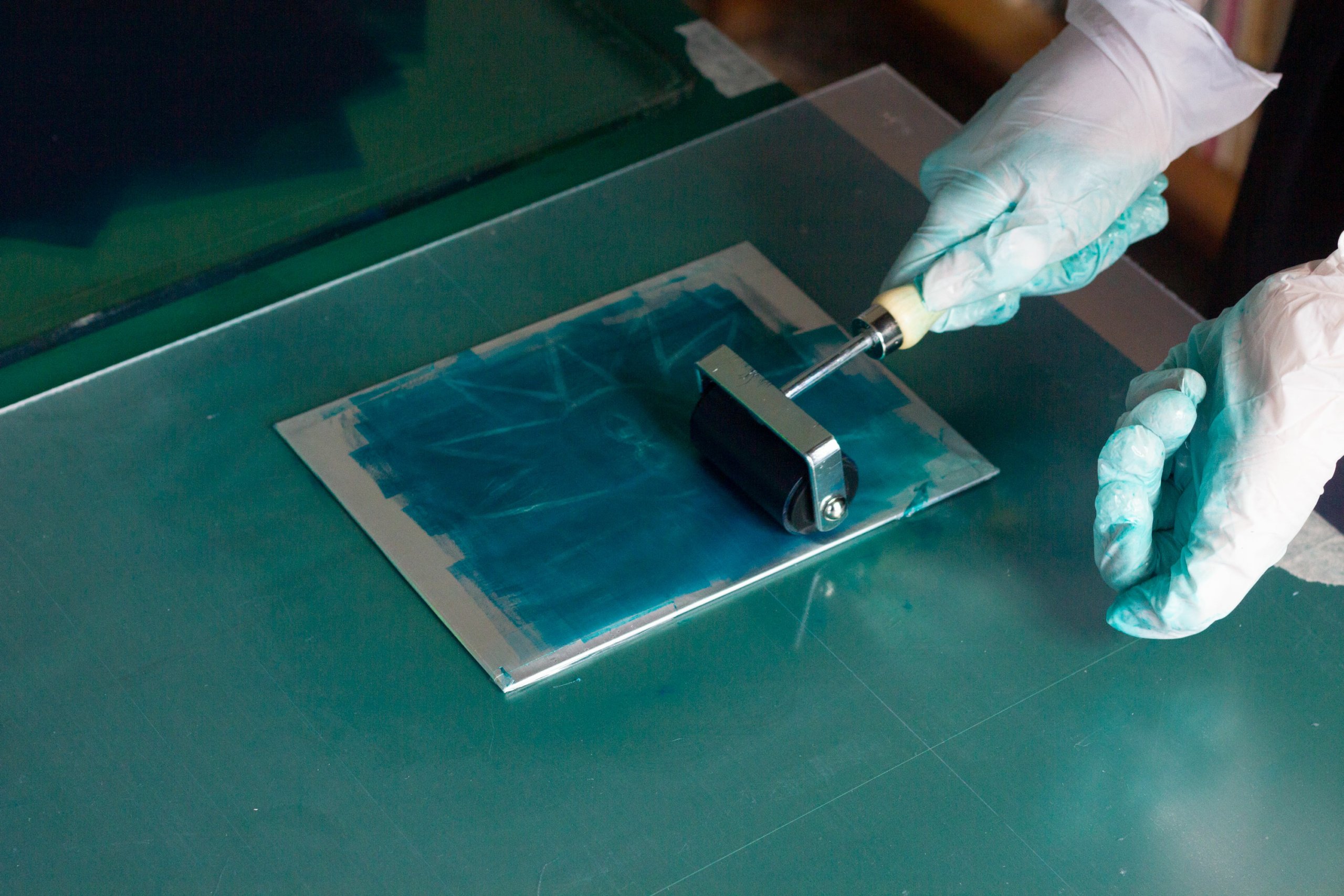
Before inking, a wet (but not dripping) sponge or cloth is passed over the plate, and only then is the ink passed over with the roller. No need to worry if, especially on the first pass, the ink also settles in the non-sensitized areas, just use the wet cloth again and pass it very gently over the drawing: the sponge will remove the ink only in the undrawn areas.
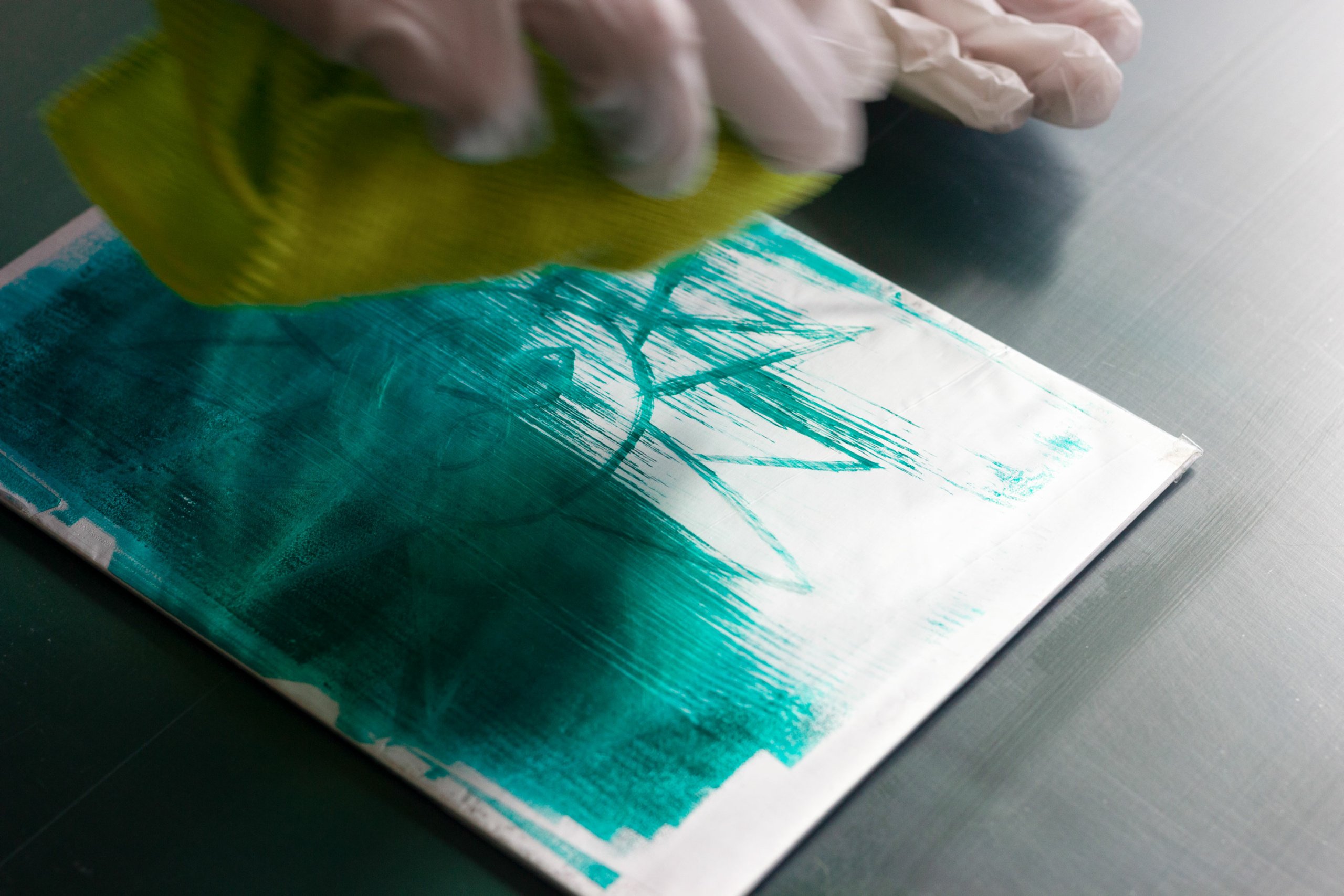
If too much dry ink concentrates on the plate at some point, wiping a cloth with a little vegetable oil will remove any residue.
6.Print
Ideally, at this point, you should have a printing press (in this case the plate must be plastic), but it is not essential. Good results can be obtained simply by laying the sheet over the plate and pressing, perhaps with the help of a spoon or potholder. To avoid ruining the paper by rubbing, you can place a sheet of baking paper over the printing paper.
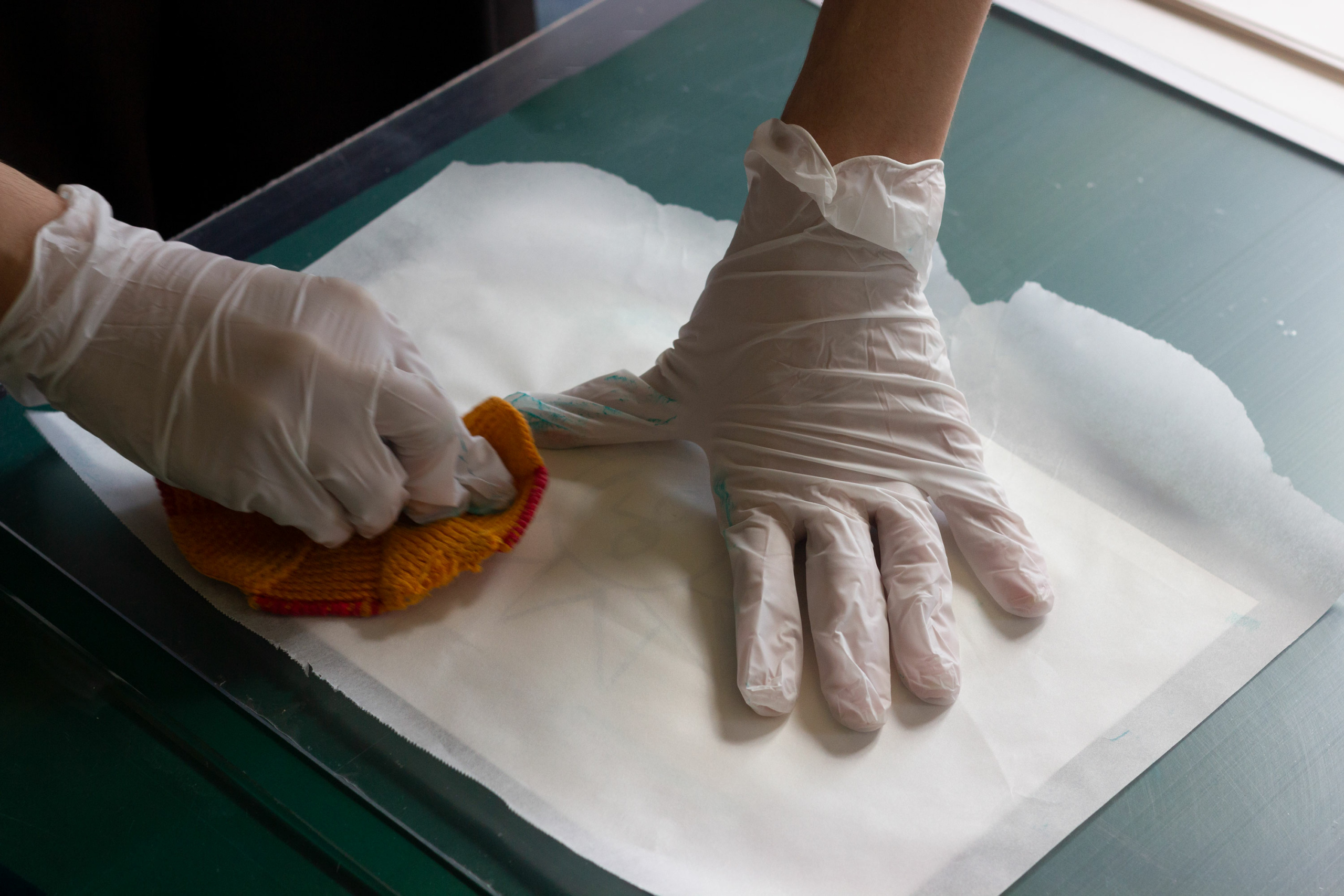
The sheet will produce about a dozen prints before it begins to lose quality.
The quality of the prints is certainly informal: the stroke is not sharp and precise, and it happens that color is deposited where it should not, but the result is very spontaneous and not easily replicated by other techniques. Keeping in mind the style of the prints, one can think of a matrix design that is not too refined and detailed, but rather benefits from a somewhat “dirty” stroke.
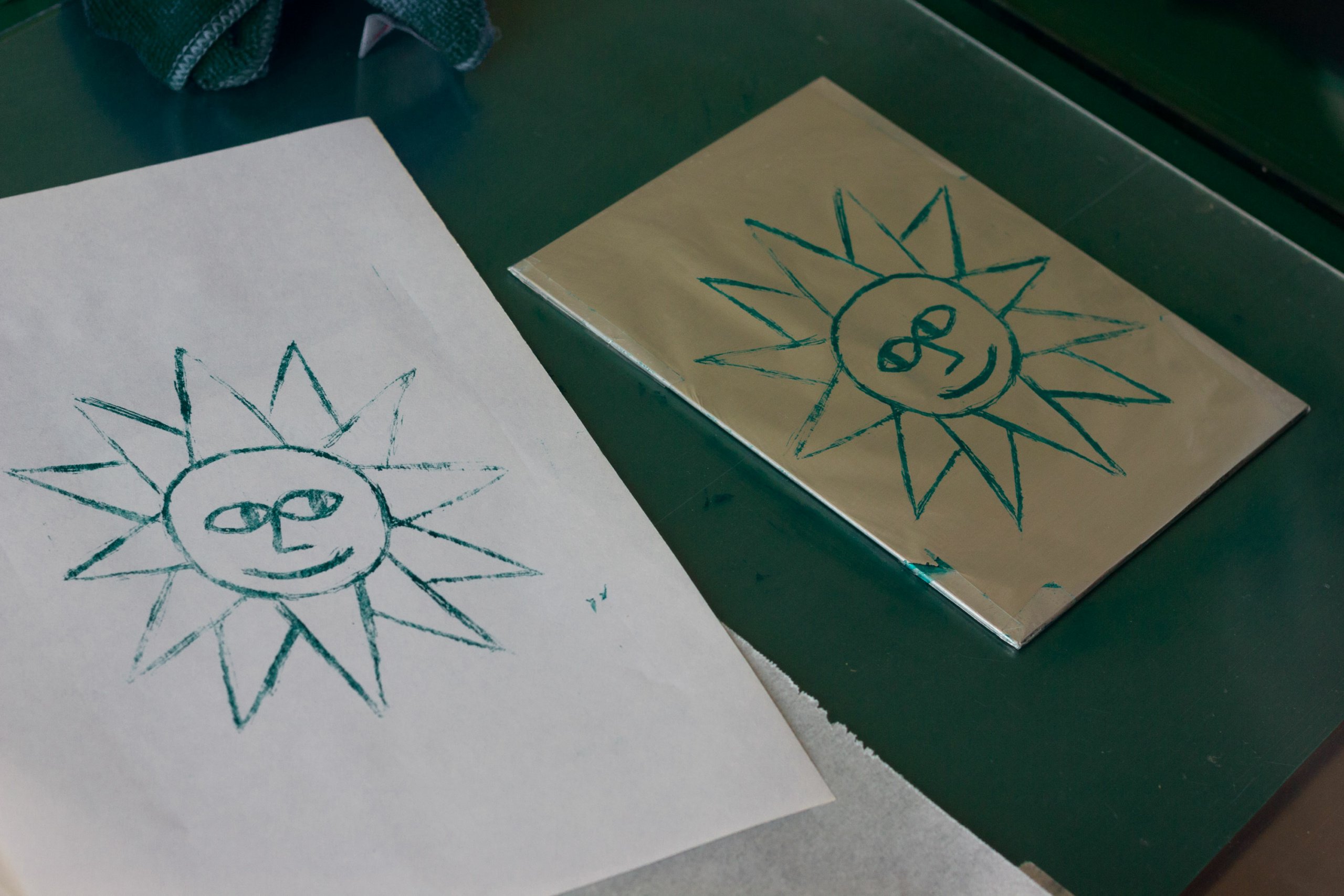
Have fun and good “kitchen lito” to all!